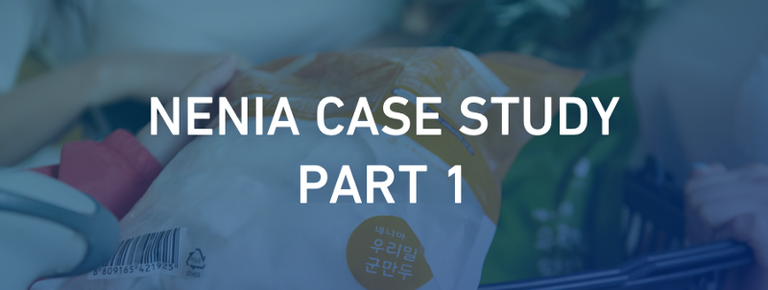
Hello, Everyone! This is TEMCO!
TEMCO is always improvising and continuing its innovation for technological advancements. TEMCO and NENIA, working together to change the supply chain world.
TEMCO and Nenia conducted a real use case study involving the use of TEMCO’s blockchain based platform prototype. We proceeded with our use case by performing a pilot test on Nenia’s current supply chain management system that utilizes ERP. Partnering with Nenia, a producer/retailer of eco-friendly organic products, TEMCO linked all the information from the initial product production stage to final delivery step using blockchain.
The TEMCO Solution
TEMCO is developing a blockchain based supply chain management platform. By using blockchain technology, segregated supply chain network is connected under one platform. Utilizing the data stored in the blockchain, TEMCO offers an analytics tool to businesses, helping them make better strategic decisions on their supply chain management processes. For consumers, TEMCO provides real-time supply chain management information and an e-commerce market with cryptocurrency transaction capabilities.
Nenia’s Current System and Opportunities
Nenia had the ideal infrastructure for our pilot test because the company directly manages the entire supply chain processes of their products. However, under the current system, it is not easy for Nenia to visualize connected supply chain and deliver eco-friendly image to consumers. To strengthen the competitiveness of Nenia’s specialty, TEMCO suggested blockchain technology that allows all the participants of the supply chain to access the journey of Nenia’s products.
The Pilot Test
The pilot test of use case consisted of 3 phases:
Pilot Phase 1: Manufacturing Facility: QR code generation & product information registration
Pilot Phase 2: The Distribution Center: Product Transfer
Pilot Phase 3: Company-owned store in Bukchon: accessing product information
Pilot Phase 1: Manufacturing Facility: QR code generation & product information registration
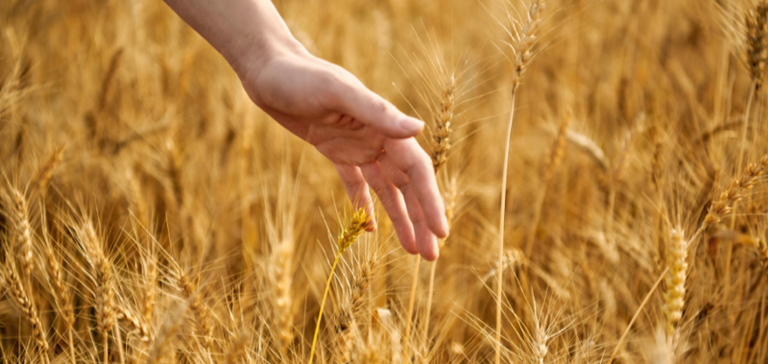
All Nenia’s products are sourced from organic ingredients. One of the most popular items is “Woori-mil dumplings”, which is made from 100% pesticide-free Korean wheat and antibiotic-free pork.
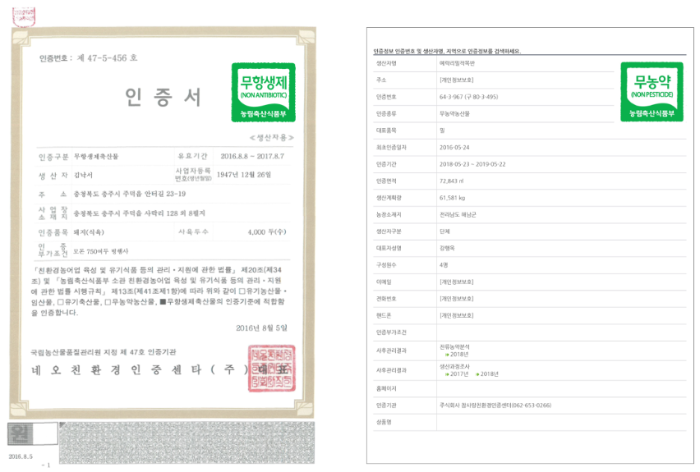
TEMCO and Nenia, as a start, uploaded raw ingredient information about “Woori-mil dumplings” into the blockchain.
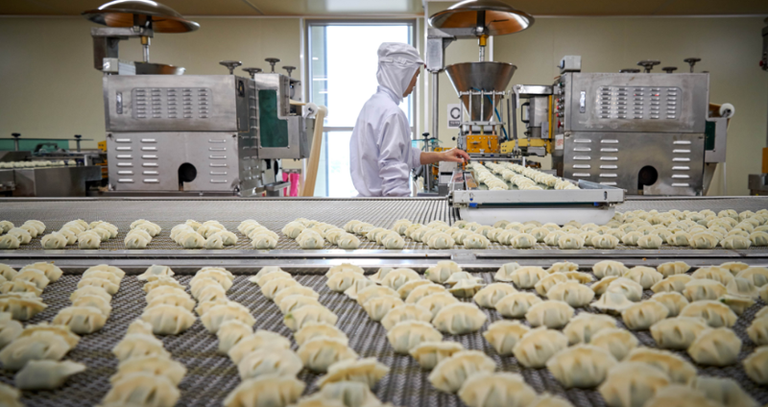
Verified by data stored in the blockchain, organic raw ingredients are transformed into reliable food products through an eco-friendly manufacturing process. All products go through HACCP guidelines and manufactured in a sanitary and quality-controlled environment. The products are packaged in the same manner, increasing reliability and quality of Nenia’s products.
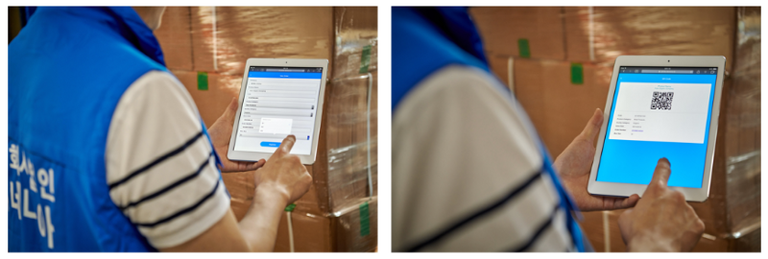
The current labeling system shows antibiotic free, organic ingredients and couple of important product quality information on the packaging, but there is a limit to providing more detailed information effectively to the consumers. However, with the utilization of blockchain technology, product name, product code, quality certification (organic, pesticide free, GAP etc.) and other major information related to the product can be shared, so that consumer’s awareness and accessibility of the environment-friendly product can be increased.
Also, the QR code that is used for uploading information into the blockchain can easily be made through TEMCO’s vender application. After the QR code is created through the application, it is printed and placed onto the specific product or the box, so that information about the product can be recorded and verified.
Pilot Phase 2: The Distribution Center: Product Transfer
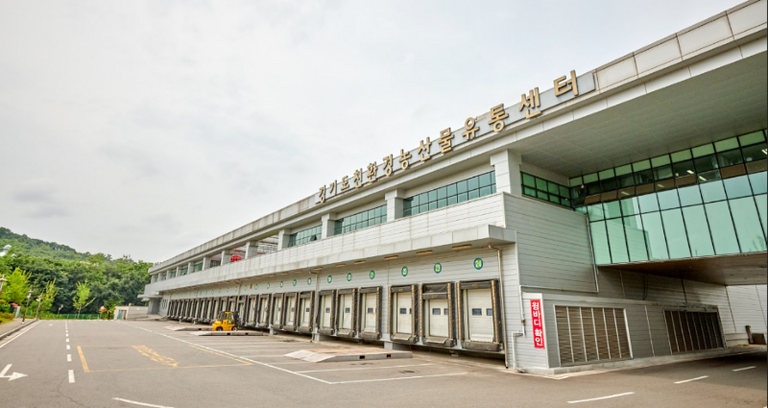
All manufactured products are shipped to the Nenia’s distribution facility in Gwangju, Korea. Since all Nenia’s products do not contain chemical additives, they are usually refrigerated or stored in the freezer.
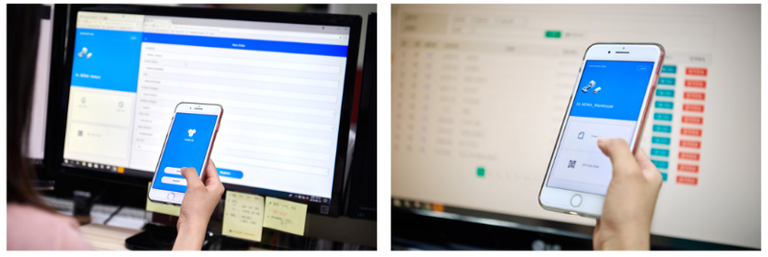
As the products arrive to the distribution center, they are stored and maintained under a strict guideline using ERP. However, using blockchain to store all the information including inventory records enables Nenia to efficiently manage their inventory and quality control process, without incurring extra cost and effort.
The Products in the distribution center are shipped out to the company-owned store in Bukchon, Seoul and grocery markets when orders come in. In a case of the frozen products, they are packed with dry ice, so that they don’t melt until they arrive to the retailers or to the consumers. After the packaging process, the blockchain based QR codes are placed on the packaging or boxes, which will have all the data connecting from manufacturing of the product to the storage, and the storage to ship out stage, all in one.
After the products are packaged, the shipments undergo a final quality evaluation before getting shipped out. Such process further increases consumers’ trust in Nenia’s products and their brand.
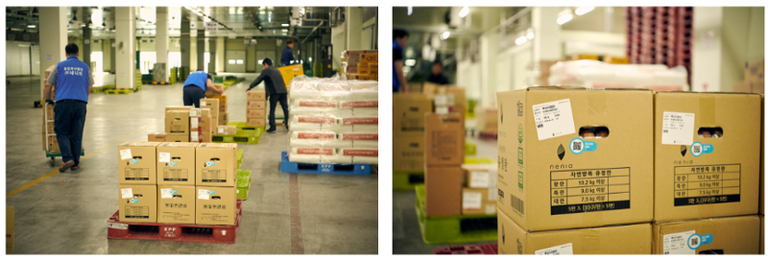
Pilot Phase 3: Company-owned store in Bukchon: accessing product information
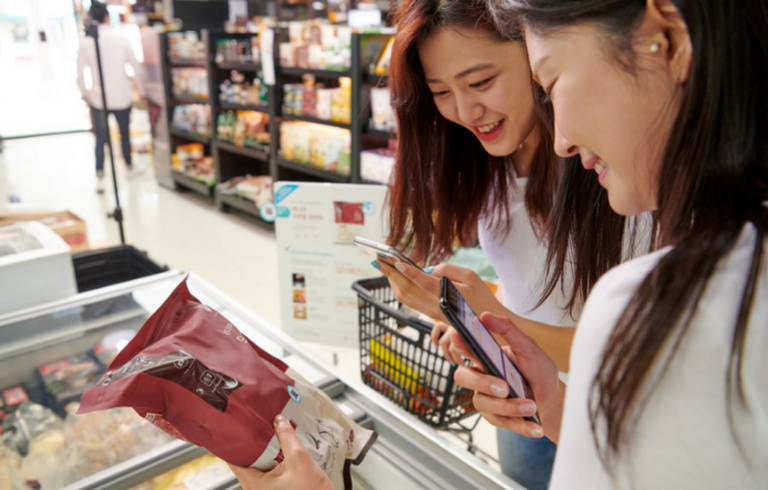
Using TEMCO’s smartphone application, consumers now have access to product information in detail by scanning the QR code attached to the product packaging. From the manufacturing process until the product is lined up on a shelf, the information saved in the blockchain increases the reliability of Nenia’s products and consumers can feel comfortable purchasing the product.
By applying TEMCO’s solution, Nenia experienced an opportunity to effectively build on their value and implement their supply chain management process into fully integrated blockchain based system.
Through Nenia’s use case, TEMCO confirmed that production, distribution, and supply chain processes can be monitored in real time using blockchain. Part 2 of the use case will continue in the next article!
TELEGRAM/ KAKAOTALK/ FACEBOOK/ TWITTER