Yesterday, March 18, marked the "2020 Global Recycling Day", a day set aside to celebrate the importance that recycling plays in preserving the earth’s primary resources, including water, air, coal, oil, natural gas and minerals. The cerebration of this day is aimed at campaigning for people to seek out ways ways of putting the planet first by considering recyclable materials as resources rather than waste.
After it's launch in year 2018, "Global Recycling Day" is in its third year and was celebrated all over the world with the theme: " #RecyclingHeroes " with an official hashtag being #GlobalRecyclingDay hashtag.source
I was much more encouraged to share this piece after reading a documentary of the celebration of the Global Recycling Day by the Lagos State University. Recycling waste is what assures of us of a clean environment and good economic value can be drawn. From bio-degradable to solids, waste recycling has the potential of adding much more value to humanity, the economy and mother earth.
Pictures of Recycled Refrigerator into a Compact Moisture Regulator (for Fish preservation) by my Infinix Hot 7 Camera
The Burden for the Recycled Machine (Fish Moisture Regulator)
Above are the images of a Compact Heater and Cooling Machine recycled from an old refrigerator. The machine was designed by myself and fabricated by my research students to regulate moisture in agricultural materials. The design became necessary as I observed the rate at which local fish dealers were losing their valuable sea foods to poor preservation. Some of the farmers dealing on fresh fish need cold preservation while those with dry fish need drying.
On trying to create a solution for the fish dealers, there was need for a compact system which perform the dual operations of cooling and drying. When the feasibility study for the design ensued, I discovered that going for new parts would become so costly that the local fish dealers would not be able to afford. After due considerations of hygiene, construction cost and material of construction, the recycling an old refrigerator became an option.
The machine enhances dual processing operations of cooling and drying simultaneously. Electrical energy is used to compress the pressure of a fluid to reduce the temperature of an enclosure, hence cooling. The heat within the cooling system is absorbed and evaporated as heat energy which is utilised for drying operation in another enclosure. The two process help to preserve and reduce the moisture level of stored products in the two enclosures respectively.
All parts incorporated into the designed were sourced locally and fabricated locally to the pictured finishing. Below is an array of some component of the recycled machine as well as pictures during the build of the machines as screenshot from my PC gallery.
Facts and Briefs on Recycling
I cannot agree less the words of Engr. Afolasade Nubi of the University of Lagos who posited that "The Earth throws back at you what you throw away, so RECYCLE”.source. Recycling is a key part of the circular economy, which helps to protect our natural resources. Statistics has the ‘Seventh Resource’ (recyclables) saves over 700 million tonnes in CO2 emissions each year and this is projected to increase to 1 billion tons by 2030.source With this, we are hopeful that the future of the planet can be salvaged by conscious recycling.
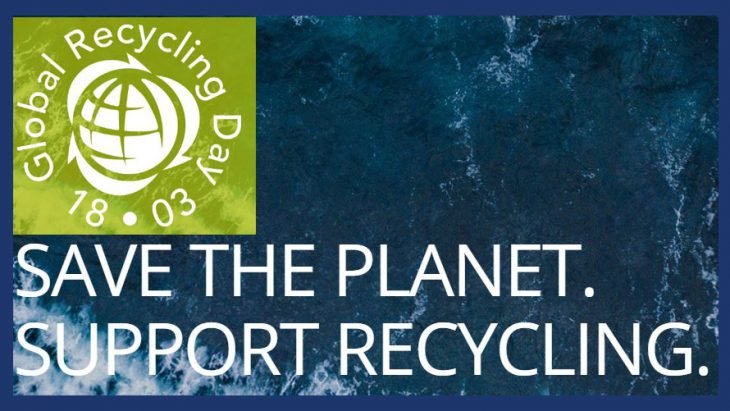
We cannot undermine the the importance that recycling plays in preserving our precious primary resources and securing the future of our planet. Recycling is geared at restoring planet earth to its original form where natures operations are not altered by human activities. Steps to cleaning the earth by recycling could be as simple as reusing an empty plastic water bottle to package another fluid or a more complex one as captured in this write. By recycling, we give more value to our products and commodities.
Description of the Compact Moisture Regulator
The machine has a dual performance capacity of cooling and drying. The agro-product moisture regulator operates using the principle of energy conservation. Heat energy dissipated in the cooling process is utilized for drying operations. The moisture regulator consists of the cooling chamber, drying chamber, condenser, compressor, evaporating valve, casing, lagging material and trays.
The drying section of the agro-product moisture regulator is a passive dryer which consists of a heat collection section for preheating the air and a drying chamber at the top to which a chimney was attached. It was constructed with metal sheet and chicken net. The cooling chamber evaporator was utilised as the heater for drying. The total dimension of the dryer was 400×250×400 mm.
The drying trays were constructed of chicken wire mesh and wood to allow air to pass through the food sample and to prevent pieces of the dried products from falling into the lower parts of the drying chamber. The lower parts of the drying chamber (desiccating chamber) was separated from the drying section by a space to allow even distribution of heated air.
Access to the drying chamber is via a small door, and the chamber has two drying trays. The door was made to be as air tight as possible. The chimney is a hollow cylinder, 0.1m in diameter and 0.5m tall and was constructed with 1.0 mm thick metal sheet and painted malt black to obtain elevated temperature to improve airflow and increase buoyancy. The chimney is covered with a cap to prevent rain and dew from entering the chamber.
The constructed cooling chamber of the moisture regulator has a handling capacity of 0.0756m3 within a temperature range of 10oC to 15oC. Some part s of the machine are described below.
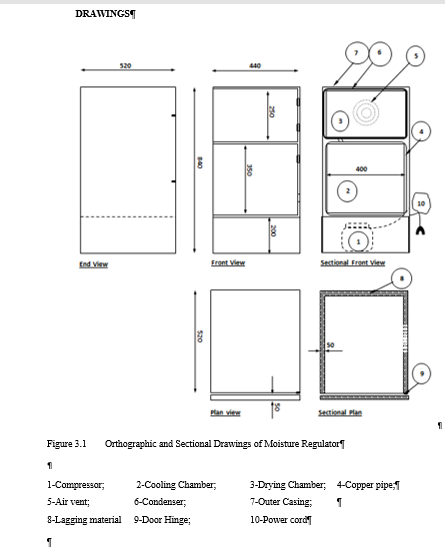
1. Evaporator
The evaporator is the machine part used to receive the liquid refrigerants from the condenser through throttle valve and to evaporate it. It is also called as cooling unit or freezing unit. It is located within the cooling chamber.
2. Compressor
The compressor is a component in the pre-cooler that is used to draw the refrigerant from the evaporator through suction valve at low pressure and to force it to the condenser through exhaust valve at high pressure and temperature.
3. Cooling Cabinet
The cooling chamber provides the handling surface for the handling of materials. It is made of wood with a polished surface which contains the bulk of vegetables to be preserved.
4. Condenser
This is used to condense the refrigerants at saturation temperature from vapour to liquid by transferring its latent heat to the water.
5. Expansion valve
The expansion is the part of the machine that is used to control the rate of admission of refrigerants to the evaporator. As the refrigerant expands in the valve, it looses its pressure and temperature at its exit end and gets cooled.
6. Lagging column
The lagging column is a 50 mm thick insulation material that helps to conceal the temperature of the cooling chamber. The column is packed with cork material to ensure that the temperature within the cooling chamber is maintained.
7. Outer lining
The outer lining of the pre-cooler is a galvanised plate used for the coating of the outer surface of the machine.
Principle of operation of the Machine
The operation of the machine follows a cycle which consists of an evaporator unit, a compressor unit, a condenser unit and an expansion valve. Ideally, heat should be transferred in the condenser and evaporator without pressure differences. That is, there should be no heat gained or lost to the surrounding although this is not 100% applicable to the real life operation.
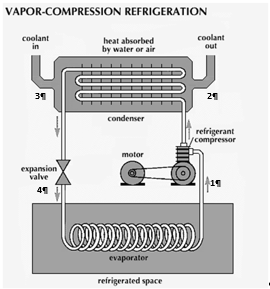
The refrigerant leaves the evaporator at point 1 as a low pressure, low temperature saturated vapour and enters the compressor where it is compressed reversibly and adiabatically (isotropically). At point 2, it leaves the compressor as a high pressure, high temperature super-heated vapour and enters the condenser where it is condensed at constant pressure. The boiling point of the refrigerant is now higher than the temperature of the surrounding air; therefore the gas gives up heat to the surrounding.
At point 3, the refrigerant leaves the condenser as a high pressure, medium temperature saturated liquid and enters the expansion valve, where it expands irreversibly and adiabatically (constant enthalpy). At point 4, it leaves the expansion valve at a low pressure, low temperature, low quality vapour and enters the evaporator, where it is evaporated reversibly at constant pressure to the saturated state at point and the cycle continues. The machine cools material to a temperature range of -30oC.
Final Words
I am embarking on more research to increase the temperature range of the drying chamber of the moisture regulator for optimized usage in drying fresh fish and other materials with higher moisture content. I will be glad to share outcomes of the research with you shortly.
References
- https://www.isri.org/news-publications/engage/2020-global-recycling-day
- https://unilag.edu.ng/?p=6197
- https://www.globalrecyclingday.com/
- https://en.wikipedia.org/wiki/Vapor-compression_refrigeration
- Onwualu, A. P., Akubuo, C. O. and Ahaneku, I. E. (2006): Fundamentals of Engineering for Agriculture. Immaculate Publication Limited, Enugu, Nigeria.
- Aworh, O. C. (2010); Reducing Postharvest losses of Horticultural commodities in Nigeria through improved Packaging. A publication of the World of Food science. Available online at http://www.worldfoodscience.org/cons/
- Harris, N. C. (1987). Modern Air Conditioning Practice (3rd edn.): McGraw-Hill Book Co., New York.
- Redlinger, Patricia (2011): Freezing: Fruits and Vegetables. Sarah L. Francis (Ed.) Iowa State University fact sheet, Available at www.extension.iastate.edu/store
@tipu curate
Upvoted 👌 (Mana: 25/30 - need recharge?)
hey, do you know what happened with sportstalk ? I saw you investing in it and the price went to 0. I also was powering up everything. Do you think that its price will recover somehow ?