I suppose there is no short answer to that since it will always depend on the context. However, if I were to venture a short answer anyways, it would most definitely be yes!
I have recently had the opportunity to experience this first hand in regards to a project we do at my work. I work at a private, nonprofit research company and our main focus is on software development.
We do however also have projects related to robotics, and IoT (Internet of Things) and similar areas.
Quite a few of our projects employ some sort of sensor based data aquisition, and that entails deploying large amounts of sensors in various situations. Usually it is something like setting up (non-intrusive and anonymisized) wifi sniffers at festivals to try and map the traffic.
We also use rfid chips and similar.
recently we got the assignment to deploy a number of small sensors to shopping carts. The sensor itself is the size of a coin but it had to be protected from prying fingers and water so we asked different companies how much that would cost. and ended at 200,- danish kroner a piece (we needed app 250 pieces)
it turned out that if I designed a small box which can be screwed together and fixed to the cart with strips, large enough to hold the sensor as well as a small(5 dkk) watertight capsule, we could get them printed at app 60 dkk a piece at a local print service.
So thats what we did. I measured the sensor, made a preliminary design and did a test print, this took about 3 hours of my time (not counting the actual time the printer ran, only my time)
We got a usable box which can be easily modified to fit our needs and lives up to our requirements much more than a bought version, and at a better price, so yes it is viable for runs up to around 200-500 pieces. more than that and I would think injection molding would probably be the cheapest.
This is the reason why I am currently working on setting up injection molding at home, but more on that in a later post.
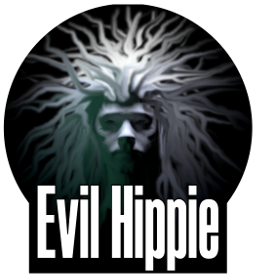
Thanks for reading this. Im EvilHippie, a compulsive creative and jack o' trades. If you want to know more about me, check out my introduction post here
If you like what you see, feel free to upvote, follow and resteem.
If this post is more than 7 days old , consider upvoting one of my newer posts instead.
or you can check out these recent posts
If you are interested in my miniatures, you might also consider visiting my shapeways shop
I doubt fused deposition will replace injection molding in most applications. Speed, quantity, finish, materials, etc. all favor injection molding in most applications. That said, 3D printing is perfect for prototyping, making certain shapes that cannot be practically molded, embedding different materials, and in small-scale production. But if yoy can get injection molding up and running at home, you jave the best of both worlds at your disposal. Vacuum forming can also be built fairly easily for a home workshop, and 3D printing can be a good way to make your mold, depending on what you need.
I agree that fdm in particular and 3d print in general wont replace injection molding, but i was surprised at what apparently constitutes a "small batch production" when up to several hundred pieces is considered small, then it is no longer just for prototyping. I myself is more inclined to get myself a benchtop injectioon molder and then (resin) print(and possibly cast) my molds than doing actual production with printers, but that is mostly because of the mechanical properties and the choice of material it gives me. not so much because it cant be done. oh and because I would have to do it myself and then a few seconds per piece in a confined time period is more convenient than going down to empty and restart the printer every X hours.
For small production batch (<1000 parts) it is interesting. I hope affordable material strong and heat resistant enough will come so that you can print the injection mold and run small batch at home. Maybe watercooled mold and some good insulator/release agent put in the mold will be enough for a small batch.
This is already doable. look here for an affordable way of getting injection molding up and running. the life time for the molds are quite limited, but it is fairly cheap to print more than one. it will only cost the resin cost. The reason why resins are the right choice here is that thermoplastics will always have to be extruded at a higher temperature than what the castings are done at. resin on the other hand is not hardened by heating and cooling and so can have very different heat resistance
Yes, they are very interesting resins. I think we will see more MIM style solutions coming on the FDM market, I hope to see an affordable one.
To the question in your title, my Magic 8-Ball says:
Hi! I'm a bot, and this answer was posted automatically. Check this post out for more information.
If you figure in the cost of the mold on the injection molding the printed numbers will be a lot higher. The main strength of injection molding is quantity production costs, but the mold is Thousands of dollars to produce and maintain.
The change over to a different part for 3D printing is a lot easier too! You could print all the parts for an assembly, one at a time, and make four assemblies, when they are ordered, with zero inventory.
:)
True. there is other consideration as well though. like time. I did a quick calculation of my capacity at home and it is app one piece pr hour plus removing prints and setting up again every 6 hours, so it would be a few days to print them. Casting and injection molding is a lot faster. There is also the strength of the parts. even though 3d printed parts are surprisingly strong, injection molded parts are stronger. but I agree, I could probably have set the numbers even higher
Valid printing time problems. Mine is slow too, but unattended time is free, and is there a practical problem with ten, or a hundred units running in parallel?
There are beginning to call this additive manufacturing and there is no reason this need be done with plastic. I troubleshoot flame spray equipment in use now, that deposits metal powder, through a hydrogen flame, onto aircrraft landing gear, to raise up the surface. This old gear, is then ground back to original specifications and returned to service!
The technology is in use now.... :)
3D printer made by people repairing turbines and similar pieces
This can enable different materials on thin layers, this is really interesting. https://www.beam-machines.com/products/magic-3d-printing-machine.
Nice toy! Maybe a little high for garage use, but very nice! Here is a filament that will work in Our printers, and allow the use of the lost wax process to cast what ever metal you want to match the printed part.
:)
Direct metal printing is still a game for the select few, but printing for casting is very much doable. I have been doing quite a few masters for sandcasting and though I have not tried it yet I have all the equipment for doing investment casting from prints
Excellent! I got some Delft Clay from Rio Grande, that acts like sand casting, but is Very fine for detail. I need to order the ceramic dip coating, but ready on everything else.
Wax printing just looks fun! I can get hot enough for steel, but not stainless yet.
It will be interesting to see if 3d printing matures to the point where it's feasible for large production runs over other methods like casting and injection molding.
I know for a fact that coloplast , a big danish medical supplies producer, is alreay using 3d printing , not only in their development, but also for initial production runs. 3d printing will probably never beat injection molding when the piece count is in the tens of thousands, but it just might for runs of a few thousand pieces. and then there is the possibility of making the molds from 3d printed metal(or some other heat resistant and durable material). I think that will definitely see some use.
Yeah, a lot of the people I've heard talking about commercial 3d printing as an alternative to traditional manufacturing talk about metal printing, either as a way of making molds or making personalized items that are a little nicer than the norm.
The Creative Crypto is all about art on the blockchain and learning from creatives like you. Looking forward to crossing paths again soon. Steem on!Hello @evilhippie, thank you for sharing this creative work! We just stopped by to say that you've been upvoted by the @creativecrypto magazine.