INTRODUCTION:
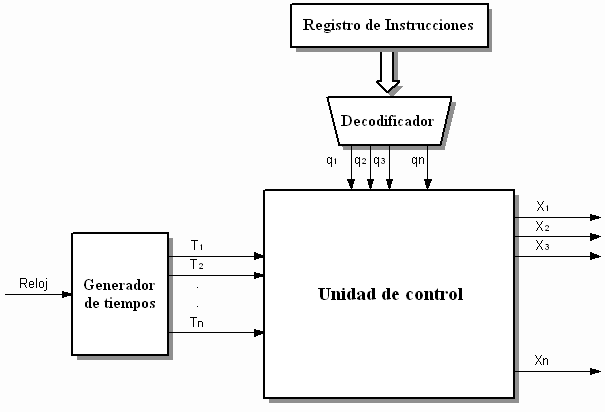
At the same time, with the development of the control sequence, a list of microoperations to be started is made for each control state. The control sequence and the transfer relationships between registers can be deduced directly from the specification in words of the problem. A time diagram clarifies the time sequence between the different control signals of the system. In a sequential circuit with clock, the clock pulses synchronize all operations including transition signals in the control variables.
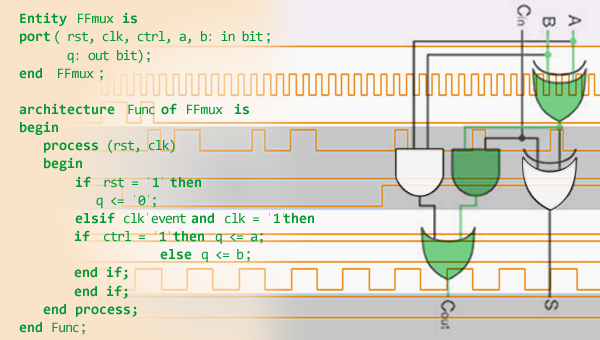
Control logic:
It is the set of logical operations and control structures that determine the order of execution of the instructions of a program. In the model MVC Model Vista Controller the data, the user interface and the control logic are the three levels at which an application decomposes.
Thus, in a web application with dynamic sheets that consult a database and display it through a browser, the user interface is the HTML representation code of the page, and corresponds to the View. The existing data in a database corresponds to the Model, and the control logic is the set of instructions that must be executed to access the searched data. The control logic can be written in different languages and executed both on the client and server or both at the same time. In the MVC paradigm, the control logic corresponds to the Controller.
Importance of Control logic:
It is important to know that the control logic is presented from a digital system that requires a control sequence beginning with the assumption of the availability of time variables. Each variable is designed in the sequence by means of a state and then a state diagram is formed.
At the same time, with the sequence development of the control logic, a list of microoperations to be started is made for each control state.
The control sequence and the transfer relationships between registers can be deduced directly from the specification in words of the problem the control logic is majority in the acquisition processes that depend on a single system.
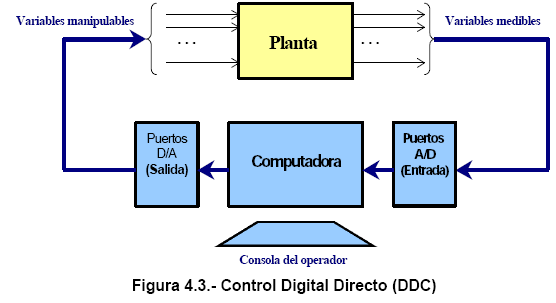
Control logic design:
The process of logical design is a complex task. Computer-aided systems are currently used to automate this process, however the development of the same and the analysis of the system can not be automated and require the mental reasoning of the human designer. The most complicated part of this process is the development of algorithms and processes to achieve the desired objectives. This depends on the creativity and experience of the designer.
An algorithm is a procedure to obtain a solution to a problem describing the steps systematically exposed. A designed algorithm is a procedure to configure the problem with a given piece of equipment. The process of developing a designed algorithm can not begin until the designer is sure of two things. First, understand the problem completely and second, you must assume an initial configuration of the equipment to conform the procedure. From these two things an algorithm is formed. The algorithm is enunciated by a finite number of well-defined procedure steps.
Operation to the control logic:
The basic and primordial function of the control logic has evolved over the years to include the control of the sequential relay, motion control, process control, Distributed Control Systems and network communication. The handling, storage, processing power and communication capabilities of some modern processes are roughly equivalent to desktop computers.
A programmed LC-link combined with remote I / O hardware allows a general-purpose desktop to be used to impersonate some controllers in some applications. Regarding the feasibility of these logically based desktop logic controllers, it is important to keep in mind that they have not generally been accepted in heavy industry because desktops run less stable operating systems than active components, and because desktop computer hardware is typically not designed to the same levels of tolerance to temperature, humidity, vibration, and longevity as the processors used in control logic.
Types of signals Associated with the control logic:
The digital signal: is a type of signal generated by some type of electromagnetic phenomenon in which each sign that encodes the content of the same can be analyzed in terms of some magnitudes that represent discrete values, instead of values within a certain range. For example, the light switch can only take two values or states: open or closed, or the same lamp: on or off (see switching circuit). This does not mean that the signal is physically discrete since the electromagnetic fields are usually continuous, but in general there is a way to discretize it univocally.
Digital systems, such as the computer, use logic of two states represented by two levels of electrical voltage, one high, H and one low, L (High and Low, respectively, in English). By abstraction, these states are replaced by zeros and ones, which facilitates the application of logic and binary arithmetic. If the high level is represented by 1 and the low level by 0, we speak of positive logic and in the opposite case of negative logic. It is worth mentioning that, in addition to the levels, in a digital signal there are the transitions from high to low and from low to high, called the falling edge and the rising edge, respectively. The figure shows a digital signal where levels and flanks are identified.
Control: The signals are captured in order to control the process, that is, to keep the variables within set values. Three parts are required: Input of variables, an algorithm of control and Output of signals of action towards the control variables to correct the controlled variables.
The type of signals used in process control depend on the level at which we place ourselves. Thus, at high level communication signals are used between PCs or field buses, while at a lower level the signals are voltage or current from readings of variables or actions on valves, relays, etc. In the field of industrial control, two types of systems are differentiated:
Monitoring: The signals are captured in order to have information on the status of the process. The process is not controlled, that is, there is no action to modify the conditions. Mainly used inputs, reading variables, except some alarm activation output if necessary.
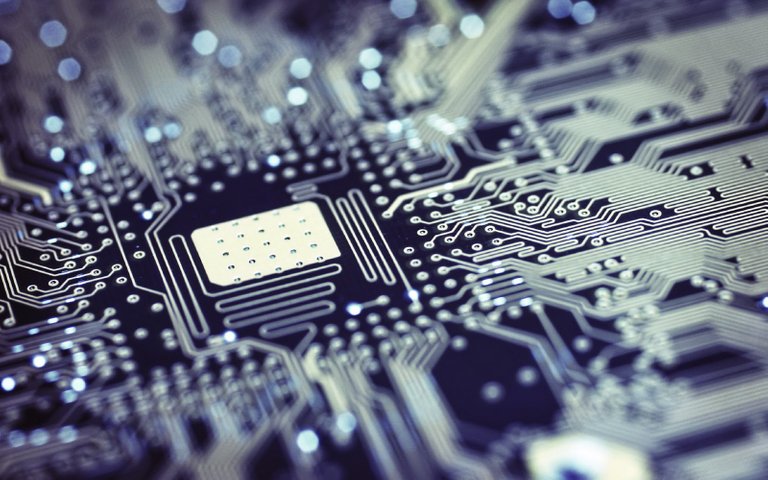
Example of a control logic associated with an industrial process:
The logic of control is largely associated with industrial processes, thanks to which numerous factors are carried out in industrial processes whose main purpose is to transform raw materials into a final product. During the production process of these goods, there are various processes, whether the materials are reused, or energy is converted to produce the final product of the logic.
Although there are several industrial processes and none is identical, it is important to know that the principles applied in the processes are similar in their principles. A process can be described as the sequence of changes in a substance.
The sequence of changes can occur in the chemical, physical or both in the composition of a substance including parameters such as flow, level, pressure, temperature, volume, acidity and specific gravity, as well as many others. Also many processes require transfer of energy.
Mixing fluids, heating or cooling substances, pumping water from one place to another, canning food, distilling gasoline, pasteurizing milk, and converting sunlight into electrical energy can all be described as processes. When a substance is heated, its temperature and composition can change. When sunlight is converted to electricity, physical changes such as chemicals can occur.
Process control through the use of (PLC):
The PLC for its special design features has a very wide field of application. The constant evolution of hardware and software constantly extends this field to meet the needs that are detected in the spectrum of its real possibilities.
Its use is mainly in those facilities where a process of maneuver, control, signaling, etc. is necessary. , therefore, its application ranges from industrial manufacturing processes of any kind to industrial transformations, facility control, etc.
Its small size, the extreme ease of its assembly, the possibility of storing the programs for their later and rapid use, the modification or alteration of the same, etc., means that their efficiency is mainly appreciated in processes in which such needs occur. as:
Reduced space
Periodically changing production processes
Sequential processes
Variable process machinery
Complex and extensive process facilities
Centralized programming check of the parts of the process
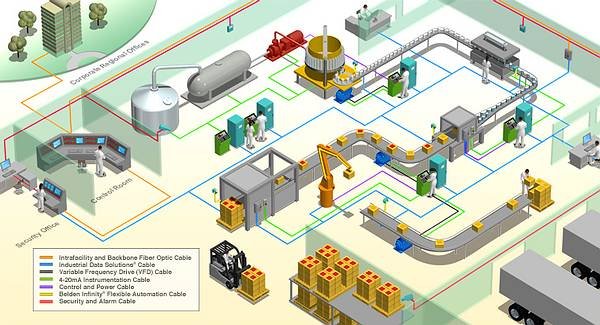
Types of industrial processes:
Process is understood as any systematic development that involves a series of ordered steps, which are closely related to each other and whose purpose is to reach a precise result, in general the development of a process leads to an evolution in the state of the element on which this treatment is being applied until this development comes to an end. In this sense, the industry is responsible for defining and executing the set of material operations designed to obtain, transform or transport one or more natural products.
It is always important to bear in mind that in order to carry out the processes, it is important that these are adequately raised. In the case of industrial and technological processes, these require a high margin of research, as well as infrastructure, which solves the Research expenses, tactics and streamlining the development process of these is why it is important to invest in projects for their application in society.
With the development of series production with assembly lines for automobiles and household appliances, and the seemingly unlimited invention of more machines for all kinds of tasks, the acceptance of innovations by the more advanced countries became a way of life in itself. Industrial societies were transformed quickly thanks to increased mobility, rapid communication and a large amount of available information.
Some types of Processes
Technological Processes
The act of inventing, creating or producing an object that meets satisfying needs, involves a series of stages, which are developed sequentially and planned.
Every technological process comprises a series of actions that are undertaken according to the development of the object that is to be produced.
Developments in Industrial and Technological Processes Since ancient times man has been developing different activities and tactics to facilitate life, these activities are the development of processes. Processes are a set of activities linked together to achieve the same goal, be it industrial or technological.
Technology helps us solve the problems and needs that surround us. Whatever the problem we face, the steps that are followed to resolve it are almost always the same.
The Technological Process.
The technological process consists of the following phases:
- Identify the problem or need.
- Explore the ideas and design the different solutions that come to mind.
- Plan the work.
- Build the object.
- Check if it works correctly.
Some technological inventions of the nineteenth and twentieth century, such as the telephone, the radio, the motorized car and the airplane served not only to improve life, but also to increase the universal respect that society in general felt for technology. These devices greatly improved the development of life in society, with which communication between different people who were at a distance very far from others became easier.
Which helped them to know other cities and go see and know other technologies and then develop them in their city. Other important inventions were the automobile, radio, television and telephone that revolutionized the way of life and work of many millions of people.
With the development of mass production with assembly lines for automobiles and household appliances, and the apparently unlimited invention of more machines for all kinds of tasks.
Identify the instruments for the measurement and control of the industrial process:
Sensors
They are the elements that detect or sense changes in the value of the controlled variable. They are often called primary elements and in some cases they are part of a block with the so-called transmitter or the one that receives the sensor output and adapts this signal for the purpose of transmitting it; This set is called a transducer.
In general, the response of a sensor determines how well the measurement, recording or control of a variable will be carried out; and its selection is the result of knowing well the characteristics of a process. Some of the most important characteristics of a sensor or transducer that define the quality of these are accuracy, linearity, resolution, etc. Another important aspect is the so-called response time or time necessary for the device to deliver the final information. To the extent that this delay can be minimized, there will be better process control.
Transmitters
Transmitters are instruments that capture the process variable and transmit it remotely to a receiving instrument, be it an indicator, a recorder, a controller or a combination of these. There are several types of transmission signals: pneumatic, electronic, hydraulic and telemetric. The most used in the industry are the electronics which have been replacing pneumatics as signals applied to these equipment over time; Hydraulic signals are occasionally used when high power is required and telemetric signals when there are large distances between the sensor and the receiver.
Pneumatic transmitters
They generate a linearly variable pneumatic signal, from 3 to 15 psi (pounds per square inch) for the field of measurement of 0 -100% of the variable. This standard signal was adopted in general by the manufacturers of transmitters and pneumatic controllers in the United States.
In countries that use the metric system, the 0.2-1 kg / cm2 signal is used, which is equivalent to approximately 3-15 psi (1 psi = 0.07 kg / cm2). The mentioned pneumatic signals are currently applied mainly as input signals to control valves or their positioners.
Electronic transmitters
These transmitters are called intelligent generate several types of electrical signals of direct current and digital signals. Among the first, the most used are 4-20 mA and 0-20 mA and panel 1 to 5 V. The electronic signal from 4 to 20 mA has a sufficient level of compromise between the transmission distance and the robustness of the equipment . Being continuous and not alternating, eliminates the possibility of picking up disturbances, is free of parasitic currents, uses only two wires that do not require shielding and allows to act directly on milliamperimeters, potentiometers, analogue calculators, etc.
Digital transmitters
They have a number of advantages over analogue ones, as we will see later On the other hand, the increasing use of digital signals in these transmitters will at some point determine the standardization of a digital protocol as it has been until now the analog signal of 4-20 ma.
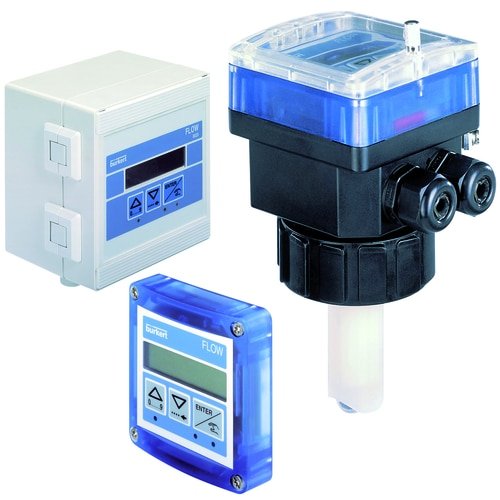
Controllers
As mentioned, the controller determines the actions necessary to maintain the variables of a process in the desired value (process controller) or it can also be the one that ensures the necessary production sequences based on a pre-established program ( PLC). We are going to refer here to the first of them.
A process controller (or regulator) can be defined as a device that compares the value of a measured variable (input signal) to the desired value (set point) to produce an output signal that maintains the desired value of the variable and use that difference to manipulate the controlled variable. The technology of these equipment has varied from tires, hydraulics to electronics, which are currently used.
</ center>
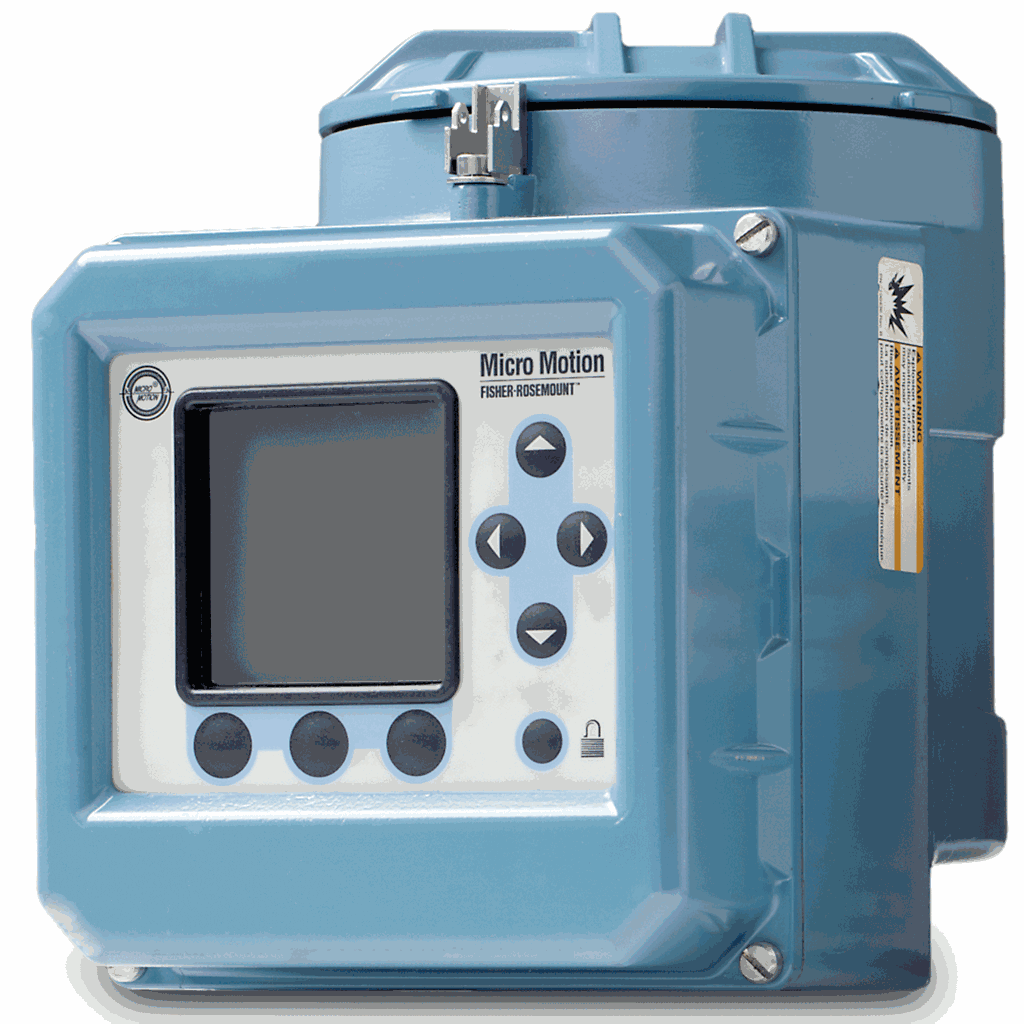
CONCLUSION:
Para concluir diremos que la utilización de la lógica de control de sistemas tiene sus ventajas y desventajas, y por lo tanto hay que conocerlas y analizarlas, entre otras plantearemos las siguientes:
• Con los sistemas basados en la lógica de control se pueden evaluar mayor cantidad de variables, entre otras, variables lingüísticas, no numéricas, simulando el conocimiento humano.
• Se relaciona entradas y salidas, sin tener que entender todas las variables, permitiendo que el sistema pueda ser más confiable y estable que uno con un sistema de control convencional.
• Se puede simplificar la asignación de soluciones previas a problemas sin resolver.
• Es posible obtener prototipos rápidamente, ya que no requiere conocer todas las variables acerca del sistema antes de empezar a trabajar, siendo su desarrollo más económico que el de sistemas convencionales, porque son más fáciles de designar.
• Se simplifica también la adquisición y representación del conocimiento y unas pocas reglas abarcan gran cantidad de complejidades.
• Por todo lo anterior, que por un lado puede ser una ventaja y por otro un posible riesgo, los sistemas basados en la lógica de control requieren mayor simulación y una excelente depuración y prueba antes de pasar a ser operacionales.
• Podríamos resumir que la utilización de la lógica de control es aconsejable para procesos muy complejos, es decir, cuando se carece de un modelo matemático simple o para procesos altamente no lineales.
BIBLIOGRAFIA:
Http://www.slideshare.net/dhayzon/transmisores-industriales
Http://es.wikipedia.org/wiki/Lógica_de_control
Http://unefacarupano.foroactivo.com/t4-tema-3-diseno-de-logica-de-control-las-pregubntas-dictadas
Http://lorenita2028.blogspot.com/2011/09/ieee-8022-control-de-enlace-logico.html
Http://www.taringa.net/posts/info/10213748/Control-de-los-Instrumentos-de-Medicion.html
Saludos, hasta pronto! @borcast