Mining and it’s effects on the environment

SURFACE MINING
MINING OF MINERAL RESOURCES
The earth’s crust contains many different types of minerals. A mineral can be a pure element or a combination of different elements. The minerals in the earth’s crust are found embedded in Rocks. A rock that contains valuable minerals is called an ore. Nearly three-quarters of the earth’s crust is made up of two non-metals:
• Oxygen
• Silicon
Silicon is found in a compound called Silicon dioxide and is commonly known as sand. The rest of the earth's crust is made up of mainly 6 metals.
Many of the elements that are of interest to us are not evenly distributed in the lithosphere. In places where these elements are abundant, it is profitable to extract them through mining. Humans are particularly interested in the ores that contain metal elements and also in those minerals that can be used to produce energy. Some of these minerals are rare and precious as such as gold, diamond and platinum but others are more ordinary, such as quartz. Like all substances, minerals are composed of elements. Some minerals can be used in their natural form such as sand and diamonds.
MINING THE ORE
The mining process starts once a deposit of a mineral of a suitable size is found. In ancient times mining and mineral processing were very primitive and the main method used to extractor ores was digging by hand. A number of different techniques and now used to mine gold and other minerals.
The three most common mining methods panning, surface mining and underground mining:
1. Panning
PANNING FOR GOLD IN A CREEK BED
Panning for gold is manual technique that is used to sort Gold from other sediments. Wide shallow pans are filled with sand and gravel from river beds that may contain gold. What is added and the pan so that the gold is separated from the rock and other material. Gold is denser and settles at the bottom of the pan.
2. Surface Mining (open pit mining)
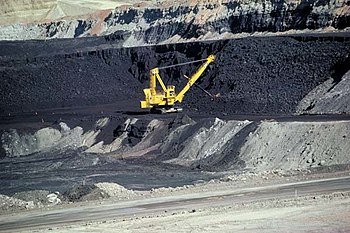
SURFACE MINING FOR COAL
In open pit mining, the topsoil is removed from the surface of the Earth. The surface layers of rock are then removed to expose the deeper and more valuable mineral layers. The valuable rocks are then blasted into smaller rocks using explosives. The rocks are loaded onto huge trucks and taken away for further crushing and processing. Any mineral that is found close to the surface can be mined using surface mining techniques. Coal and copper are mined in this way.
3. Underground Mining (shaft mining)
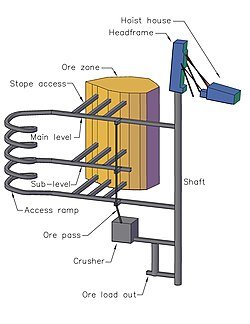
A MODEL OF AN UNDERGROUND MINE WITH SHAFT ACCESS
If minerals are found deeper, underground mining is used. After drilling, blasting and equipping a mine shaft, tunnels about leading out rates from the main shaft to the ore deposits. Shaft mining is a very delicate operation, Andrew supports I needed so that the rock does not collapse. The intense heat and high pressure inside the shaft and tunnels make shaft mining very dangerous.
REFINING (EXTRACTING) MINERALS
Ancient methods of refining metals
Ancient people soon learned that fire could be used to refine and purify metals. This is the earliest method used to extract minerals from the ore. Archaeologists have found evidence of iron processing sites that date back thousands of years. Between 1100 AD and 1800 AD people use Iron to make Spears and farming tools.
To extract the iron from the ore, people mixed charcoal and iron ore and heated them in a pit. The oxygen in the ore combined with the carbon from the charcoal to form carbon dioxide and the iron was left behind. This process is now called smelting.
Modern process of extracting iron from iron ore
A BLAST FURNACE
Once the ore has been mined, it is crushed into smaller pieces to make extraction of the iron easier. Smelting involves heating the crushed ore to a very high temperature, often in a blast furnace.
• The three raw materials, iron ore, coal and limestone, are poured in at the top of the blast furnace
• Extremely hot air, which is required to start the reaction, is blasted into the furnace. A reaction temperature of 1000 degrees Celsius is required
• The carbon in coal produces carbon monoxide which, when combined with high temperatures, converts the iron oxide into liquid iron metal. The liquid metal sinks to the bottom of the Furnace and is poured off into moulds. The iron at this point is called pig iron
• Limestone is then added to absorbed all the impurities. The limestone, together with the impurities forms a waste material which floats on the surface of the molten iron and is removed. The waste material is called slag. Slag can be used to make roads
• The molten iron is poured into moulds and left to solidify. This Iron is called cast iron and is used to make railings and storage tanks. The rest of the iron is used to make steel.
THE END
REFERENCES
1.https://en.wikipedia.org/wiki/Mining
2.https://en.wikipedia.org/wiki/Gold_panning
3.https://en.wikipedia.org/wiki/Surface_mining
4.https://en.wikipedia.org/wiki/Underground_mining_(hard_rock)