A race to 3D print anything
The time has come when houses can be built in 24 hours. By injecting materials and having a digital model of your desired structure 3D printing has given us this opportunity and will revolutionize the housing industry. Starting with Apis Cors - who brand themselves as a company that print buildings. Apis Cors recently announced that they successfully 3D printed a 650-square-foot home in 24 hours. To be clear, in one day a roof, walls, and the interior were assembled by a robot on site. Printing these massive structures on site reduces the price tremendously due to the lack of transportation costs incurred on the material.
3D Printed Austin, Texas home
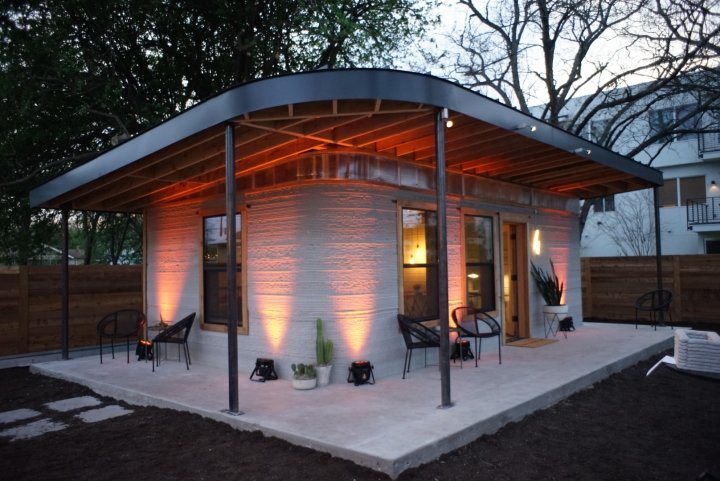
Show me the competition?
HuaShang Tengda
Chinese construction company, HuaShang Tengda completed an even more impressive task back in 2016 by printing a two-story 400-square-meter home on site. The assembly of the house took a month and a half slashing the status quo for construction time by months. The largest 3D printed home actually belongs to HuaShang Tengda's competition, WinSun.
HuaShang's 3D printed home
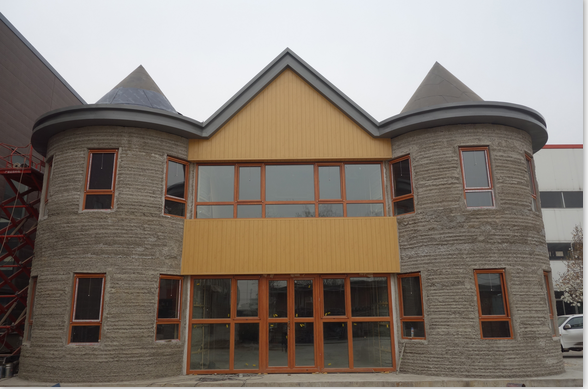
WinSun
WinSun has managed to 3D print an entire apartment building, consisting of six stories, as well as an impressive home, which certainly doesn’t appear to be 3D printed by any means. Please reference the photos below. These structures were unveiled at the Suzhou Industrial Park, of east China’s Jiangsu Province, and the apartment building alone features a structure which is approximately 1,100 square meters in size. The 3D printer took about one day per floor to construct using a sort of paste recycled from waste material. Using a machine which measures 20 feet tall, 33 feet wide and 132 feet long, the engineers at WinSun started with a basic CAD drawing which they used as input to the 3D printer that was able to fabricate the structure piece-by-piece using a specially formulated and patented ‘ink’. The ink, which includes construction waste such as concrete, fiberglass, sand, and a special hardening agent, is an incredible way to recycle general construction materials — not to mention it is flexible, self-insulating, and resistant to strong earthquakes. The walls and other components of the structure were fabricated offsite with a diagonal reinforced print pattern and then shipped in and pieced together. The company then placed beam columns and steel rebar within the walls, along with insulation, reserving space for pipelines, windows, and doors.
WinSun's 3D printed mansion
WinSun's 3D Homes

I wish we'd spend more money researching on things like this rather than weapons of mass destruction.
All the possibilities this could do in the future, we won't be just reusing wasted material we'll be building a sort of economy of just wasted or recycled materials. 3D printing has come a long way since it's dawn and we could implement this feature on other things.
Built with paste from waste materials.
That doesn't sound reassuring.