For a long time now I have wanted to build robots. I have all the prerequisites in place I know the theory and have access to the tools. Even so, there are some things that makes it more difficult than it should be.
The most important thing is myself. I cannot help but want to do everything from scratch. There is a lot of maker in me and perhaps a little bit of a prepper too. I do like if I know and control every part of the process.
Thus, I started with a simple project, a hand. I started with the things i know best, The physical design. My plan was to then go on to the software part (which would be more or less a copy paste thing from my PhD) and finally do the motor control.
I have worked on and off on it for a few years now and I have come a long way with the physical design. This however is only my first printed design. No motors and no controls, basically a puppethand.
I chose to build the hand as a modular design, that way it would be easier to produce, should i ever get that far with it. All the finger joint are identical, apart from the tips . The base of the hand is made from several components, which can be combined to make more or less fingers.
they can also be replaced with another base to give a different finger configuration.
I used a string to actuate the fingers, and while this gives less control over each individual joint , it drastically reduces the degrees of freedom, which means I need fewer motors to control it.
The idea is that the flexing of hte fingers are done by the motors and the straightening is done by a passive spring. this means that i have control over the grib strength while again reducing the control parameters.
On a finished model the joints would consist of a pin made from e.g. aluminium, but for this early prototype pla was fine. I used graphite(from a normal pencil) as the lubricant . Many types of plastic dont like oil very much, so graphite is a great lubricant for these.
I learned a lot from this early experiment. For one, the hand was far to big compared to what it needed to be, so I downsized my later versions. the fingers where made from 3 parts per joint, which were glued together, and this was real overkill when doing prints. I did it to cut down on the need for supports but I have become better at orienting and designing my prints to get around that problem so i can get by with 1 or 2 parts per joint.
There was also a few good things in this version which I would take with me for the next iterations. The way the wires where drawn through the joints was quite well functioning. No hard corners where the could get stuck etc. The fingers joints was pretty solid so that was good too.
All in all it was a great success and, as one of my early printing experiments, it was quite good. I have learned a lot since then, as I will show you all, in a later post. I hope you like it
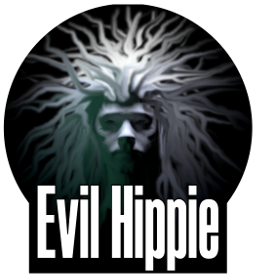
Im EvilHippie, a compulsive creative and jack o' trades. If you want to know more about me, check out my introduction post here
If you like what you see, feel free to upvote, follow and resteem
or you can check out these recent posts
wintertrees
delegation
dragon part 2
dragon part 1
ram it
screw it
Congratulations! This post has been upvoted by SteemMakers. We are a community based project that aims to support makers and DIYers on the blockchain in every way possible. Find out more about us on our website: www.steemmakers.com.
If you like our work, please consider upvoting this comment to support the growth of our community. Thank you.
You have been scouted by @promo-mentors. We are a community of new and veteran Steemians and we are always on the look out for promising authors.
I would like to invite you to our discord group https://discord.gg/vDPAFqb.
When you are there send me a message if you get lost! (My Discord name is the same as here on Steemit)
This reminds me of that Futurama episode where Bender downgrades himself.
Can't wait to see more of this project as it develops.
thanks unfortunately futurama is still on the (very long) list of stuff I haven't seen yet.
Cool !
I discovered recently a plastic called UHMWPE (Spectra brand for instance) that will be perfect for this kind of application.
This plastic is super strong, abrasion resistant, self lubricating and it has other nice properties.
There are mono filament fish-lines made of this material that can replace strings (stronger than steel).
However I did not yet found a filament for 3D Printers, even if pellets are not so expensive.
Sounds nice. I will check it out. I have used fishlines as string on my later versions, but just normal nylon ones.
That is so cool. It kinda looked like wood but that be another level of crazy :D Looking forward for future developements with this one
Thanks, the layers of a printer looks a bit like woodgrain, especially on curved surfaces. I cannot imagine the amount of work it would have been to carve it in wood though.
Nice! Have you tried actuating it with servos yet? I've been writing the software for that on an Arduino, just for fun. Just one finger and a thumb for now, though.
No I havent, not for this one at least. I am currently involved in a research project, where we have two stepper motors running of some arduino-like boards. It is for a soft robot with string actuation, but it will be usable for something like this also. this one will not be actuated though. Too much friction in the joints, and I was not really satisfied with the design anyway. I have a version 2 which i will post about later and I am working on version 3 which i hope to hook up to some actuators
I use servos that can easily overcome friction 8-). Anyway, the force feedback algoritms are the most interesting, for me at least, especially when you try to do that without pressure measurements, but only measure current being drawn by the servos. I have a very silly application for it; it will be a remote controlled arm and hand that turn the volume knob on my old amplifier.
My InMoov robot uses also a similar technique for his hands. My problem with those cords is that it is not so reliable as I would like to have it.
I always think about designing a hand for him that doesn’t need cord to move the fingers. It’s more reliable when it would be gears between the segments somehow but I didn’t had a good idea how to do this yet.
I think the pros of using gears is better control and precision, maybe added strength too. The pros of strings are that you get an automatic load-sharing between the joints of the fingers when gripping. That goes a long way. If you went for the more exact gear solution you would loose that (or at least I cannot imagine how). The real reason is of course that it is much easier to make.
This looks like a fun project!!
Any plans for building a full human android? ;)
oh yeah lots of plans - but seriously I would like to at least make a functioning arm, taking it incrementally, and hopefully ending with a full functioning robot.
I imagine so much time, work and dedication had gone into this technology, but hey that's the price for what you have birthed today. Stay strong brother. This is the best job I have seen on the internet today.
There should be a follow through which is a second arm to legs to head until this project is complete.